Introduction
Slag vertical roller mill is the equipment to grind Ground Granulated Blast furnace Slag (GGBS) into small particles. GGBS (fineness:4200-4500cm2/g) produced by vertical roller mills are being used to substitute clinker in conventional cement manufacturing as well as to partially replace OPC for ready-mixed concrete production, for which the percentage of GGBS usage is typically at 10-15% and 20-25% respectively.
Slag vertical roller mill can be used to grind non-inflammable and non-explosive materials with Moh's hardness below 9.3 and moisture content below 6%, Such as: slag, limestone, calcite, barite,dolomite, potassium feldspar, marble, talcum, gypsum, kaolin, bentonite, medical stone, rock phosphate,iron ore, quartz, active carbon, coal, ect.
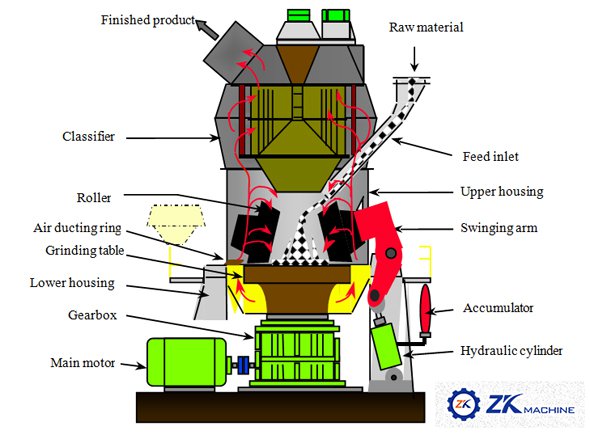
Features
1. Good return on investment
The widely use of slag increases the market demand to slag gradually. In recent years, investment in slag production line has been a new favorite in investment market. One production line can recover the cost in 1-3 years.
2. Reducing the power consumption of slag micro powder preparation effectively.
According to the display of slag powder production measured data, traditional ball mill needs power consumption 75~80kWh for per ton slag micro powder. However, it needs power consumption 42~45 kWh for per ton slag micro powder if adopts advanced vertical roller mill technology, and it can be saving electricity 33~35kWh use of vertical roller mill production per ton slag, and power saving effect is very remarkable.
3. Reducing the environment pollution effectively in the process of slag powder preparation.
Slag powder vertical roller mill adopts the internal negative pressure system to reduce the dust spillover effectively. The equipment adopts advanced technology with low revolving speed, stable operation, low noise, and the noise does not exceed 85dB(A) from the mill 1 meter.
4. Removing iron effectively, increasing additional income.
The advanced technology of slag vertical roller mill can be removed the iron effectively from the slag, and no less than 1% iron content can not only protect the machine, but also can increase additional income.
Parameter
Model |
Grinding Table Diameter
(mm) |
Roller Diameter
(mm) |
Roller Number
(n) |
Motor
(kW) |
Output
(t/h) |
GRMR22.30 |
2200 |
1400 |
3 |
550 |
70 |
GRMR26.30 |
2600 |
1600 |
3 |
790 |
100 |
GRMR28.30 |
2800 |
1750 |
3 |
900 |
115 |
GRMR30.30 |
3000 |
1700 |
3 |
1000 |
120 |
GRMR32.30 |
3200 |
1500 |
3 |
1400 |
160 |
GRMR34.30 |
3400 |
1500 |
3 |
1600 |
180 |
GRMR36.41 |
3600 |
1600 |
4 |
1800 |
200 |
GRMR38.41 |
3800 |
1700 |
4 |
1900 |
230 |
GRMR40.41 |
4000 |
1800 |
4 |
2240 |
260 |
GRMR43.41 |
4300 |
1900 |
4 |
2500 |
310 |
GRMR46.41 |
4600 |
2060 |
4 |
3150 |
350 |
GRMR48.41 |
4800 |
2240 |
4 |
3350 |
390 |
GRMR50.41 |
5000 |
2360 |
4 |
3500 |
420 |
GRMR53.41 |
5300 |
2500 |
4 |
3800 |
470 |
GRMR56.41 |
5600 |
2600 |
4 |
4500 |
540 |
GRMR59.61 |
5900 |
2600 |
6 |
5000 |
610 |
GRMR63.61 |
6300 |
2700 |
6 |
6000 |
720 |
Note: mill spectral pattern benchmark
-
Material medium friction (MF)=0.9~1.0;
-
Material moisture max 7%;
-
Refined powder granularity 80μmR 12~15%;
-
Refined powder moisture 0.5~1.0%;
-
The concrete mill installed power and technology parameter will be adjusted appropritely basing on the actual material property and requirements of owner;
-
The above specification also applies to limestone powder mill, and the concrete type selection shall be decided according to material property.