Fujian 100000 m³/a Sludge Expanded Aggregate Production Line
Project Overview:
Project Location: Fuzhou, Fujian, China
Construction unit: Fujian Luxiang New Material Technology Co., Ltd.
Product Name: Expanded Aggregate Production Line
Production scale: Annual production of 100,000 m³sludge expanded aggregate production line project
Scope of services: from the storage, transportation, drying, batching, mixing, granulation, calcination, cooling of raw materials to the finished product storage and transportation system, environmental dust collection system, exhaust gas dedusting and desulfurization system, electrical automation control system process design, plant planning, equipment supply, equipment installation and commissioning, after-sales training and other one-stop technical services.
Project Description
Fujian Luxiang Building Materials Technology Co., Ltd. is a professional enterprise engaged in the production of energy-saving building materials. The company has a fully automatic intelligent production line for the production of expanded aggregate and block, which is required to expand production to meet the market demand in 2017. After more than half a year of inspection, Henan Zhengzhou Mining Machinery won the trust of customers with excellent solutions and signed the contract in September 2017. The two sides went to the project site and the case site to conduct on-the-spot exchanges for many times, and improved the process according to the actual requirements of the owners. The overall design of the production line meets the national environmental protection requirements. In the design, the domestic advanced energy-saving improvement equipment is adopted in many places, and the original factory building is utilized as much as possible in the planning to reduce the project land. At present, the project has been installed and will enter the production phase immediately.
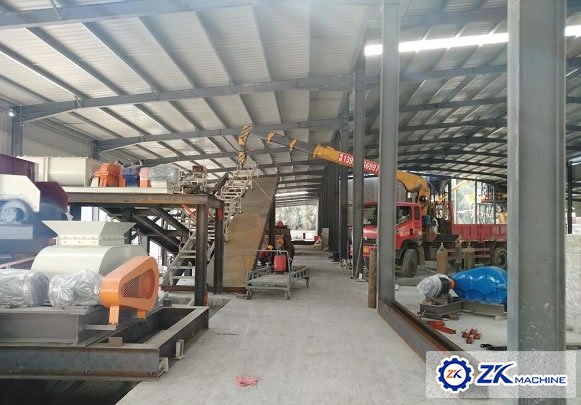
Production Process
The raw materials for the production of sludge expanded aggregate mainly include sludge, river mud, and muck.
The process of producing expanded aggregate in the production line is: raw material drying→raw material batching→aging→feeding of raw materials→mixing of raw materials→granulation→shaping screening→calcining→cooling→sieving→storage.
The sludge and clay are pre-mixed by batching, and then the mixed materials are stored for aging storage. The qualified aging materials are fed from the forklift to the box feeder. The box feeder feeds the material to the belt conveyor and then conveys it to the twin-shaft mixer through the belt conveyor for mixing. The material after being stirred by the twin-shaft mixer is conveyed to the granulator for extrusion granulation. The finished raw material ball is sieved through a shaping sieve, and the plastic sieve is screened out of the unqualified ceramsite below 5 mm, and the qualified ceramsite is sent to the cutting tube at the top of the kiln tail and enters the rotary kiln. A double gate valve is arranged at the upper end of the cutting pipe to lock the air, so that no gas overflows when the material enters the kiln tail, and the unqualified material is sieved.
At the kiln end of the rotary kiln, the flue gas is interposed into the drying kiln, and the material with higher water content is first dried, and then the flue gas is discharged into the bag filter for dust removal. The discharge density of the bag dust collector can reach below 30mg/Nm3, achieving the standard discharge and clean production. The purified flue gas is sent to the desulfurization tower for desulfurization treatment, and the flue gas after the desulfurization treatment is directly discharged to the chimney after being led to the chimney by the fan.
The rice husks that are bought from the market are generally crushed and transported to the factory and packed in uniform woven bags. After the rice husk is poured into the upper hopper, the rice husk is lifted into the rice husk silo by the bucket elevator. The rice husk in the rice husk silo is fed to the single-channel burner by means of the speed setting provided under the silo, while the primary fan provides external wind as the combustion air for the single-channel burner, and the rice husk passes through the single-channel burner and then is sprayed into the kiln. The ceramsite from the cooler is lifted up to the stockyard.
Main Equipment
No |
Name |
Model |
Quantity |
1 |
Double Shaft Mixer |
φ400×3200 |
One Set |
2 |
Double Roller Granulator |
GL800×700 |
One Set |
3 |
Plug-in rotary kiln |
Φ1.6×26m+Φ2×18m |
One Pack |
4 |
Rotary Cooler |
Φ1.5×15m |
One Pack |
Related Products
You can get the price list and we will contact you within one business day!