The airflow calcination equipment is to make the hot air flow and the gypsum powder in direct contact with the gypsum powder in the air duct, and the dihydrate gypsum is rapidly dehydrated to make hemihydrate gypsum. This kind of equipment is generally equipped with a dispersing device at the feeding end of the desulfurized gypsum. On the one hand, a high-speed rotating hammer is used to crush and throw the material to achieve particle dispersion. The particles are in uniform contact with the hot air flow to complete the heat exchange. In the process of airflow calcination, the gypsum particles are heated in a suspended state, the gas-solid two-phase heat exchange area is large, the material and the hot flue gas move in the same direction, the initial temperature difference is large, and the heat exchange efficiency is high. A cyclone is arranged to disturb the gas-solid two-phase flow, so that the relative velocity difference between the particles and the air flow is generated, and the heat transfer efficiency is enhanced. In the airflow swirl section or diffusion section, the airflow velocity decreases, which is equivalent to increasing the heat exchange and drying time between the large particle gypsum and the hot flue gas, which is beneficial to the calcination process. The main features of airflow calcination equipment are compact and simple equipment, low equipment cost and high heat exchange efficiency.
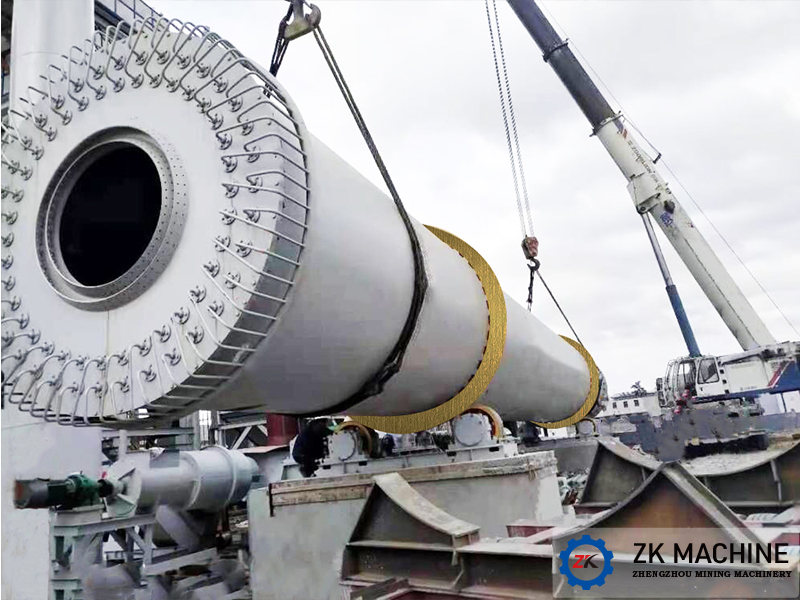
1.2 Direct heating rotary kiln
The direct heating rotary kiln is the direct contact between the hot air flow and the raw gypsum powder in the rotary kiln cylinder, and the dihydrate gypsum is dehydrated into hemihydrate gypsum. The gypsum powder rotates slowly in the inclined rotary kiln, and the heat medium generally moves in the same direction as the gypsum powder. Since the gypsum powder is partly in the accumulation state in the rotary kiln, the heat exchange efficiency is relatively low. Hot flue gas generated after the combustion of natural gas and heavy oil. The direct heating rotary kiln is generally equipped with a lifting plate or a baffle plate to ensure that the gypsum is evenly dispersed in the cylinder section and then contacts with the hot air flow, reducing the generation of wind tunnels and improving the heat exchange efficiency. At the same time, due to the high evaporation intensity and high humidity of the material at the inlet, in order to reduce the adhesion of the wet material to the cylinder wall, the temperature control of the inlet hot air flow is relatively high. The whole kiln body equipment is long and is a rotating body. The system moisture removal and dust collection are difficult to control. The advantage of direct heating rotary kiln is that the equipment structure is relatively simple and it has a price advantage.
Air flow calcination equipment and direct heating rotary kiln are used as direct heat exchange methods. The calcination process is mainly convective heat exchange between the material and the hot air flow, so that the free water and part of the crystal water in the wet desulfurized gypsum vaporize and absorb heat, and the temperature of the air flow itself drops. Heat and take away water vapor, mass transfer and heat transfer process are completed in the same airflow, so the airflow must have a certain air volume, and the exhaust gas temperature must be higher than the calcination temperature, which leads to an increase in the energy consumption of the entire system.
2. Indirect heating equipment
2.1 Continuous wok
The continuous frying pan is a circular pan with a transverse inner heat exchange tube. The heat energy is indirectly transferred to the dihydrate gypsum in the pot by the drum, the bottom of the pan and the heat exchange tube. The water produced by mechanical stirring and gypsum dehydration The steam disturbance makes the gypsum particles in a fluidized state, and the gypsum particles contact the heat exchange tube evenly to exchange heat, heat up and dehydrate to form hemihydrate gypsum, which is discharged from the pot body through the overflow port. The heat energy can be provided by the hot flue gas generated after burning coal, natural gas and heavy oil. The temperature of the material in the pot is relatively low, and the calcination time of the material is mostly about 1h, which belongs to the low temperature and slow calcination method. The continuous frying pan generally needs supporting airflow drying equipment to be applied to the calcination of desulfurized gypsum, and it is necessary to avoid the super-large-scale frying pan equipment. The influence of the arrangement of heat exchange tubes and stirring devices should be considered when selecting models. The overall cost is high, but the calcination quality is stable.
2.2 Internally heated tubular steam rotary kiln
The internal heating tube type steam rotary kiln is suitable for places with steam. Compared with the direct heating type rotary kiln, there are many heat exchange tubes inside. The steam passes through the tubes. Condenses into water after exothermic. The internal heating tubular steam rotary kiln adopts a paddle conveyor to feed the material, and moves forward with the rotary kiln rotating at a slow speed (1~5r/min). The tubes are in contact at the same time, and the heat exchange efficiency is low. The design of the lifting plate or the baffle plate can ensure that the gypsum is evenly dispersed in the cylinder section and improve the heat exchange efficiency with the heat exchange tube. The whole kiln body equipment is long, the steam system is more complicated, and the cost is high.
2.3 Internal heating tube type (heat transfer oil, steam, flue gas) boiling calciner
The internal heating tube type (heat transfer oil, steam, flue gas) boiling calciner is a vertical straight container, which adopts the principle of fluidized drying. It is to support the solid material, and at the same time, the Roots blower generates a blast air flow from the distribution plate to enter the bed evenly, and the air distribution plate can be combined with a single or multiple units; the second is that the container is arranged with a partition, and the material can be heated in a long stroke; The third is that there are a large number of heating tubes in the container, and the heat medium in the tubes is saturated steam, heat-conducting oil or hot flue gas; the fourth is that the upper interface of the container bed is arranged with a feed port and an overflow port, gypsum enters from the feed port, and after dehydration Enter another area of the baffle to the overflow outlet. The fluidization of gypsum in the whole boiling calciner is mainly realized by the steam generated by gypsum dehydration. This equipment can use low temperature or high temperature heat source, balance and dispersion of gypsum feed, heat exchange tube design, blast preheating and airflow distribution , the position and height of the internal partition, the horizontal or vertical flow direction of the heat medium, etc. are the key points to be considered in the design and application of the internal heating tubular boiling calciner. Among them, the boiling furnace with flue gas as the heat medium is equipped with an airflow drying device, which has low equipment cost, stable calcination quality and wide application.
2.4 Main features of indirect heating equipment
The heat of the indirect heating equipment is directly transferred through the material and the heating pipe, and the scouring of the material on the heating pipe eliminates most of the boundary layer on the surface of the heating pipe, reducing the heat transfer resistance and enhancing the heat exchange efficiency.
The calcination process does not require air flow and material contact heat exchange, the amount of hot and humid air discharged outside is small, and the temperature of the hot and humid air discharged outside is low, so the heat energy of the whole system can be used in cascade, which greatly reduces the comprehensive energy consumption of production.
3. Principles of desulfurization gypsum calcination process and equipment selection
3.1 The appropriate calcining process and calcining equipment should be determined according to the type of building gypsum end products. If it is used to produce gypsum building materials such as paper gypsum boards and gypsum blocks, rapid or composite calcining equipment can be selected. The building gypsum produced by the rapid method sets and hardens quickly, which can improve production efficiency and is suitable for assembly line production; if it is used to produce gypsum cementing materials such as plastered gypsum and bonded gypsum, slow or composite calcining equipment should be used. Gypsum sets and hardens slowly and has stable performance.
3.2 The appropriate calcination process and calcination equipment should be determined according to the heat source. Different equipment has different requirements for the heat source. Due to rapid calcination at high temperature, anhydrite AIII and AII will inevitably be produced in plaster of Paris products, resulting in unstable performance of plaster of Paris products. Therefore, in the presence of low-temperature heat sources such as steam or heat transfer oil, it can be given priority.
Relying on the research and development of technical equipment and the manufacture of high-quality equipment, Zhengzhou Mining Machinery is used in sludge recycling ceramsite projects, drilling cuttings, phosphogypsum treatment, desulfurization gypsum treatment, medical waste incineration, hazardous waste incineration, aluminum ash disposal, and flue ash extraction. , comprehensive utilization of coal gangue, chemical hazardous waste sludge harmless disposal and many other solid (hazardous) waste recycling business areas, providing many customers with advanced technology and special equipment manufacturing for environmental protection and resource recycling projects. Zhengzhou Mining Machinery has an experienced technical team with R&D capabilities, which can provide customers with project feasibility study, raw material analysis, formula design, small test, pilot test, environmental impact assessment report technical support, project overall planning and design, equipment manufacturing , installation and commissioning, technical training and after-sales service, etc., to provide a complete industry chain, systematic solutions.