Energy-Saving and Consumption-Reducing Measures for Cement G
Date:2021-11-10 13:21:49
Author:admin
Views:
210
1. Reduce the particle size of the clinker to be milled, adopt the "more crushing and less grinding" process, and modify the system to reduce the power consumption of grinding
The pre-grinding equipment should be equipped before the cement mill, and the particle size of the material is effectively reduced by the circular flow crushing method, so that the particle size of the material entering the mill is less than 10mm. When the material of the particle size is ground in the mill, the grinding efficiency can be improved. It can also make the particle size of the cement between 3 ~ 32μm, thereby effectively improving the quality of the product. At present, the most economical thing is to add a roller press before grinding. The structure of the roller press is reasonable and its working principle is very advanced. After the materials enter the crusher, a reasonable movement trajectory is used to make these materials achieve multi-functional composite crushing in the crushing cavity. This method consumes less metal energy and electricity. Moreover, the roller press has high reliability, and it will not randomly appear mechanical failures; it can combine the functions of crushing and grinding, with large crushing ratio, high efficiency and low power consumption. According to relevant statistics, the utilization rate of the electric energy resources of the crusher is 30%, while the utilization rate of the ball mill is only 5%. In order to effectively reduce power consumption, reduce costs, and improve efficiency, it is very necessary to adopt the process transformation of "more crushing and less grinding", which is an important measure to improve the working efficiency of the ball mill.
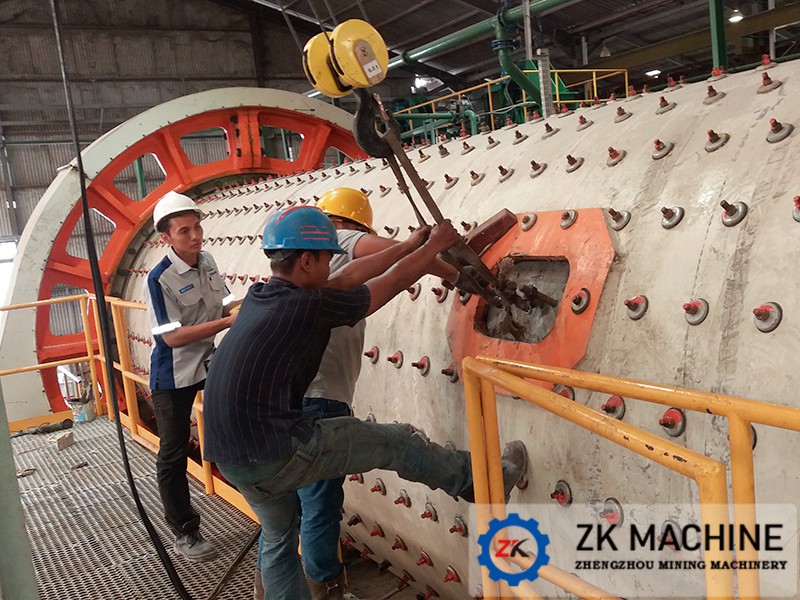
2. Improve the characteristics of cement and add more mixed materials
Usually the finished cement need to be mixed with mixed materials before they leave the factory, which can not only effectively improve the performance of cement, but also make the cement suitable for different types of engineering construction. Moreover, adding mixed materials can also save cement clinker. Saving clinker is equivalent to saving carbon dioxide, sulfur dioxide and other pollutants emitted in the production process. While saving electricity, coal and other energy consumption, which has the effect of energy saving and emission reduction. In addition, the mixed materials added can also be industrial waste residues, such as fly ash, steel slag, etc. After these industrial waste products undergo a certain high temperature treatment, their calcium oxide has become aluminate or silicate. Applied to cement production, it can effectively improve the performance of cement, reduce the particle size of materials, reduce the production cost of cement, and improve economic benefits.
3. Use suitable grinding aids
Cement grinding is the main energy consumption part in the production process of cement products. Appropriate grinding aids can be used, which can effectively improve the particle size distribution of cement, and can reduce the grinding time, reduce the particles with size less than 3μm, and increase the grinding output of the ball mill, thereby saving power consumption. Grinding aid is a new type of technology product, which can enhance performance and reduce cost. Its function is mainly realized through the grinding aid function. The grinding aid function can distinguish the cement particles, then the cement and steel balls can be distinguished, so that the fluidity of the cement can be enhanced, thereby improving the working efficiency of the ball mill, increasing the unit output of the mill, increasing the specific surface area, and effectively increasing the strength of the cement. Chemical substances, cement and mixed materials in the additives can effectively enhance the hydration products of the cement after a certain chemical reaction, improve the reactivity of the cement, and achieve the enhancement function. When cement needs to be finely ground, the effect of adding grinding aids is more obvious. For example, in an enterprise, there are two Φ3.2×13m ball mills with an output of 45-50t/set. In order to increase the output, the company adopted grinding aids and carried out technical transformation of the mill, using micro-grinding bodies to improve the grinding capacity of the mill; using small steel forging with a diameter of 8-12 mm. The total surface area is 2.5 times that of ordinary steel forging. After the technical improvement, the application of small forging has increased the output, the specific surface area of the cement product has increased, and the composition of the cement powder particles has been improved. In the end, the output of each unit was increased to 50-55t, the output increased by 10%, and the fineness was less than 2.6%.