The Role of the Second Combustion Chamber of the Waste Incin
Date:2021-05-07 08:46:28
Author:admin
Views:
154
Waste Incinerator are often used as equipment for the harmless treatment of medical waste, domestic waste, and animal harmless treatment. The flue gas produced during the calcination process of the waste incineration rotary kiln contains dioxins. The reason why the waste incineration rotary kiln is equipped with a second combustion chamber is to ensure that the flue gas stays at a sufficient temperature for a certain period. Thereby effectively reducing the content of the flue gas environmentally friendly discharge of substances such as dioxins. The state stipulates that the calcining of hazardous waste must have a secondary combustion chamber.
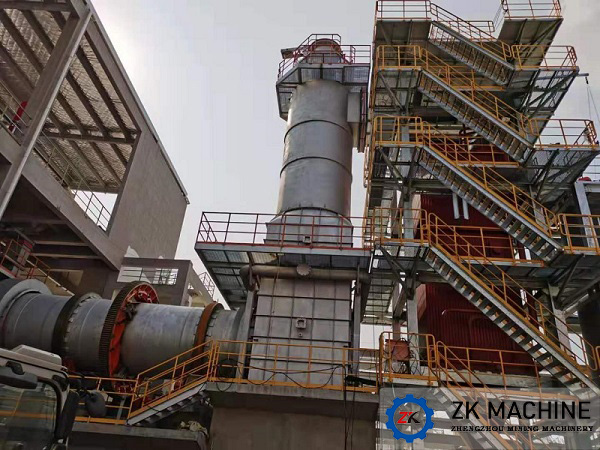
Waste incineration rotary kiln + secondary combustion chamber + tail gas treatment equipment; to achieve the secondary use of waste heat, through the hot water heat exchanger, it can be used by hot water users or recycled; tail gas is passed through the spray absorption tower, activated carbon adsorption, and high-efficiency bags purification by type dust collector; the temperature of the first combustion chamber is 850-900℃, and the second combustion chamber is 1000-1200℃; the residence time of high-temperature flue gas in the furnace is indeed greater than or equal to 2.0S; the combustion efficiency is greater than or equal to 99.9%; the incineration removal rate Greater than or equal to 99.99%; the thermal reduction rate of the incineration residue is less than 5%. The unburned hazardous materials in the flue gas are further destroyed in the second combustion chamber.
In order to completely decompose the unburned embers and meet the emission requirements, the second combustion chamber is equipped with a burner to assist combustion, and is equipped with a unique secondary air supply device to ensure that the flue gas is in full contact with oxygen at high temperatures. At the same time, the residence time of the flue gas in the second combustion chamber is ensured, and the air supply volume is adjusted according to the oxygen content of the flue gas at the outlet of the second combustion chamber. The temperature in the second combustion chamber is controlled at 1000-1200°C, and the residence time is greater than 2s, so that the flue gas can be fully decomposed and burned in the furnace, so as to achieve a higher decomposition rate. At the same time, the large-size dust in the flue gas falls into the bottom of the second combustion chamber to complete the primary dust removal. The dust removal efficiency for 40um particle size dust is greater than 90%. To prevent the dusty flue gas from directly entering the heat exchanger, large-size dust deposits on the outer wall of the heat exchanger, causing blockage.
To cool the flue gas quickly and avoid the re-generation of dioxin, a water heat exchanger and an air heat exchanger are installed behind the second combustion chamber. After the high-temperature flue gas is exchanged with the water heat exchanger, it enters the two-stage air heat exchange. The flue gas temperature is quickly reduced from 1100°C to 200°C and enters the subsequent treatment facility.