Brief Introduction of Pulverized Coal Burner
Date:2020-07-14 16:00:19
Author:admin
Views:
168
Structure of Four-channel Pulverized Coal Burner
The burner is mainly composed of pipeline, nozzle, metal corrugated compensator, butterfly valve, pressure measuring instrument and protective layer.
1. Pipeline: from the outside to the inside are the axial air channel, the cyclone air channel, the fuel channel, and the central air channel.
2. Nozzle: processed by special materials, the cross-sectional area of the outlet of the axial flow and cyclone flow can be adjusted, so as to adjust the spray speed of each wind. The entire set of nozzles is a key component to ensure the shape of the flame.
3. Metal corrugated compensator: It is the main component that connects the inner and outer pipelines of the shaft (swirl) flow wind, seals and adjusts the shape of the flame.
4. Butterfly valve: used to adjust the air volume.
5. Pressure gauge: Directly display the wind pressure in the burner pipe.
6. Protective layer: namely fire-resistant cast layer.
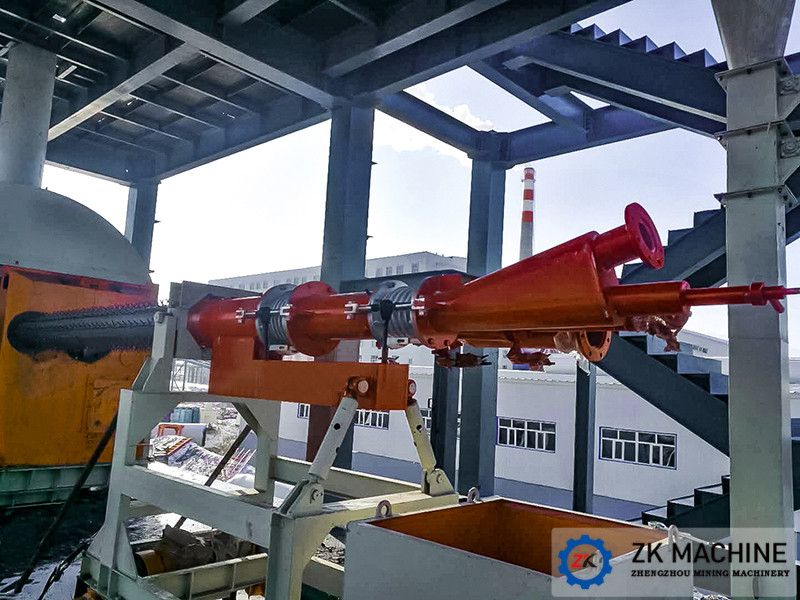
Head Structure and Working Principle
The fuel is sprayed out from the fuel channel at a certain diffusion angle, and it is transmitted to a relatively high momentum and momentum moment by the combustion air outside. The swirling wind mixes with the injected fuel and spirals forward at a high speed, and the axial wind that is ejected at a high speed. The beam meets. The insertion of the axial wind beam further enhances the mixing of fuel and wind (including the surrounding secondary air), and can adjust the degree of flame divergence. The length and thickness of the flame can be adjusted as required to achieve the desired flame shape. The role of the central wind is to promote the combustion of a small amount of fuel and CO in the central part, so that the combustion is more sufficient, and plays a role in steady flow. Because of this combustion mechanism and the high speed of the cyclone and axial winds, the combustion is very rapid and complete.
Offset Comparison Table
Rotary kiln diameter (m) |
Offset between track center and rotary kiln center(mm) |
diameter <3m |
X=50~100mm |
diameter 3~3.5m |
X=100~150mm |
diameter 3.5~4m |
X=150~200mm |
diameter 4~4.5m |
X=200~300mm |
Diameter > 4~5m |
X=300~350mm |
Note: X represents the coordinate position of the burner at the kiln mouth, and the offset direction is the material accumulation side in the kiln.
The offset value is for reference only, the specific data is subject to the data of the design institute. |
Operating Instructions of Burner
1. Preparation Before Starting
1.1 Before starting, you must read and understand the installation files of all devices, including the following:
1.1.1 Understand the operating conditions (type, flow rate, pressure, liquid temperature, etc.) of all relevant equipment and the site conditions.
1.1.2 Confirm that all parts of the equipment are installed in good condition.
1.1.3 Check the connection parts (sealing type, coupling fit, welding type conditions, etc.).
1.1.4 Turn the motor and pump by hand to check whether it rotates flexibly. Check whether the rotation direction of the motor is correct after power on, otherwise, reconnect the wiring.
1.1.5 Check whether the pressure gauge is installed well.
1.1.6 Check and test whether the external connection of the instrument and control device is safe.
1.2 Check the following items before starting the fuel ignition device:
1.2.1 Whether the pipeline connection is correct.
1.2.2 Whether all valves rotate flexibly.
1.2.3 Whether all pipelines are cleaned to ensure that there is no debris blocking the pipeline, otherwise it will cause ignition failure.
1.3 The following work should be done before the burner starts:
1.3.1 Whether all pipeline connections are completed.
1.3.2 Whether all pressure gauges are installed.
1.3.3 Check whether the position of the burner head is in the "0" position.
1.3.4 Check the position of the burner in the kiln.
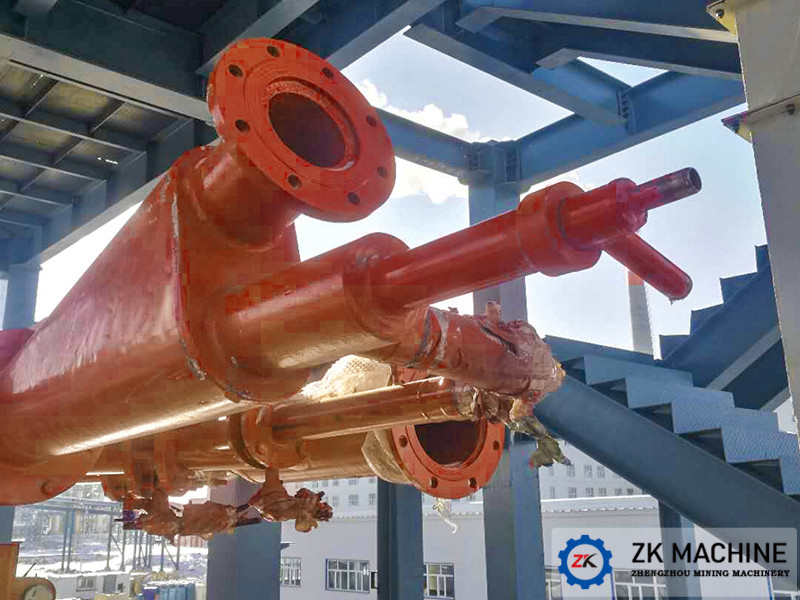
2. Safety matters
2.1 The reason for explosion or deflagration is that in a certain space, flammable materials and air continue to accumulate. After reaching a certain concentration, high temperature combustion occurs, and the exhaust gas generated by the rapid combustion cannot be discharged in time. Therefore, for safety reasons, the operation of the system should be controlled under conditions that do not produce such mixed combustion before installation and ignition.
2.2 Installation is dangerous under the following conditions:
2.2.1 Insufficient fuel combustion;
2.2.2 Sudden flameout, unburned fuel continuously enters the kiln;
2.2.3 The ignition was unsuccessful due to incomplete cleaning and blocked pipelines;
2.3 The following safe chain relationships should be strictly observed:
2.3.1 When abnormal operation occurs, all valves should be closed, and it is not allowed to open until the fault is not eliminated.
2.3.2 Sudden power failure, all valves should be closed immediately, and the fuel source should be closed at the same time.
2.4 Safety of combustion equipment
In the case of high temperature, in order to prevent the deformation and bending of the burner head and the hot section, the combustion air blower must be kept open for the next use so that there is air flow in the axial flow duct to keep the burner cool. In comparison, the required air volume is 1.5% of the primary air (minimum configuration of cooling air fan).
If the air volume in the axial air duct is insufficient, the strength of the end of the burner will be damaged and the outer casing will be damaged.
Remember: the use pressure of the meters on the pipeline and the burner should not exceed the rated pressure requirements of the fan under any conditions of use, so as not to damage the fan.