Analysis & Calcination Test of Dolomite
Date:2020-04-15 17:19:43
Author:admin
Views:
154
The chemical composition of dolomite is CaMg (CO3) 2, which is a kind of carbonate mineral of the crystal belongs to of trigonal system. Its Mohs hardness is 3.5-4 and the specific gravity is 2.8-2.9. It is not only the main raw material of magnesium production line, but also could be used for the refractory inner layer of the converter, slag making agent, cement raw material, glass flux, kiln industry, fertilizer, stone for construction and decoration, paint, insecticide and medicine, etc.
As the main raw material for silicon-based magnesium smelting in China, the chemical composition of dolomite is very important. Only if each component is correct, it could meet the requirements of silicon thermal smelting. Therefore, the analysis and calcination test of various components of dolomite and forging white in the early stage is particularly important.
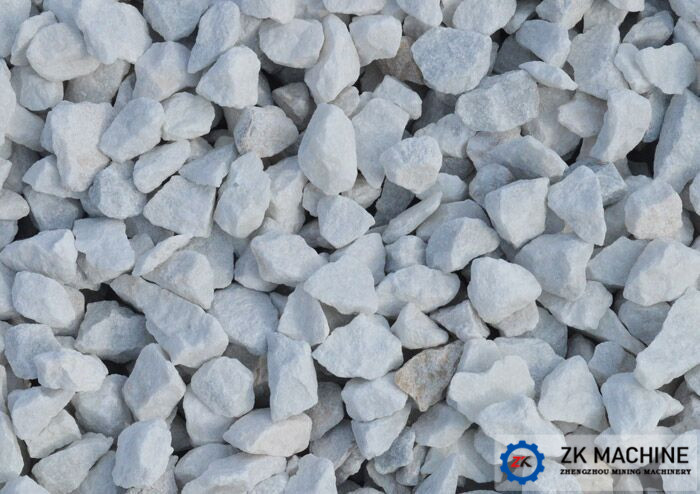
The silicothermal magnesium smelting is currently the main method used in China to produce metallic magnesium. This process grinds the calcined dolomite and ferrosilicon into a fine powder according to a certain ratio and presses it into agglomerates, which is installed in a heat-resistant alloy tank. Metal magnesium vapor is obtained by reduction under certain temperature and pressure conditions, condensed and crystallized into solid crude magnesium, and pure magnesium is obtained after refining. Henan Zhengzhou Mining Machinery Co., Ltd. has many years of successful experience in the silicon thermal magnesium smelting process. Complete laboratories and pilot lines can provide accurate preliminary data, professional production workshops, and high-quality production equipment for later industrialization lay a good foundation for production.
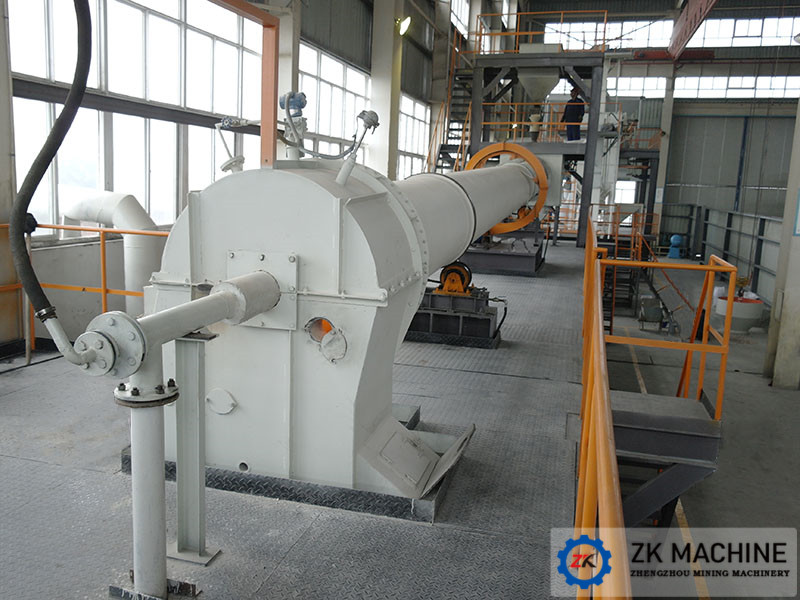
The Pilot Production Line of Henan Zhengzhou Mining Machinery Co., Ltd can imitate industrial production to calcinate dolomite materials. The specific operation is to crush the dolomite sample used in the calcination test with a particle size between 10mm-20mm and put it into a rotary kiln for calcination to control different calcination temperatures. The materials were calcined at 950 ℃, 1050 ℃, 1150 ℃, 1250 ℃, and then the materials calcined at different temperatures were collected to detect the loss on ignition, and the main chemical components were detected by X-ray fluorescence spectrometer and X-ray fluorescence spectrometer.