Brief Introduction of Sludge Ceramsite Production Line Techn
Date:2020-04-13 15:53:50
Author:admin
Views:
236
With the development of industry and the progress of human civilization, the ecological environment has suffered destruction and pollution. In terms of industry, with the development of the industrial economy, industrial waste is increasing, such as steel plant sludge, printing and dyeing sludge, and paper plant sludge. In municipal engineering, sewage treatment plants are increasing day by day, and sludge waste after sewage treatment is also increasing.
As the amount of sludge rises linearly, the problem of sludge treatment and disposal becomes particularly important. The sludge itself contains a large amount of organic matter. In the past, the main treatment methods were dehydration, incineration, and landfill. At present, due to the rise of the construction ceramsite industry, sludge has gradually developed into one of the main raw materials for construction ceramsite.
Henan Zhengzhou Mining Machinery Co., Ltd. upholds the corporate philosophy of "Morality goes before work,profit got later than others", and strives to contribute to the country's building materials and environmental protection. Through the company's technical team night and day research, simulation, experiment and other work on the ceramsite production line. Finally, a sludge ceramsite production process with high output, low energy consumption and low investment was successfully designed.
The process of our sludge ceramsite production line mainly adopts batching, aging, granulation, roasting, cooling, screening, packaging and other technological processes. The water content of sludge is generally 80%, and the bulk density is 1.1t / m³. The sludge itself has a high water content, and it needs to be weighed with shale powder, clay and other raw materials, and then mixed. The mixed materials are transferred to the aging workshop through a belt conveyor.
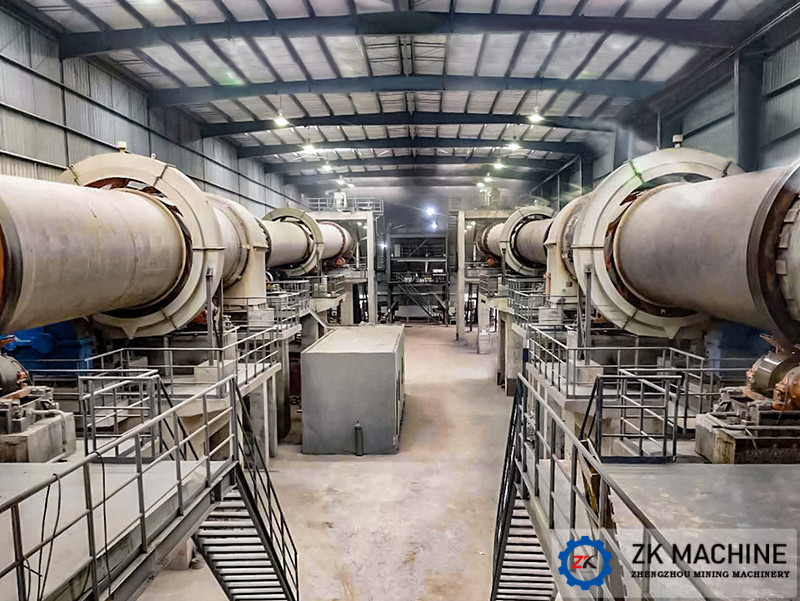
The raw materials are stored and aged in the aging workshop for a certain period of time, and then enter the granulation of the roller granulator. Qualified materials after granulation enter the drying kiln, roasting kiln and cooling kiln. The cooled finished product is transferred by bucket elevator. The ceramsite after transfer is sieved through a roller screen, and the sieving particle size can be divided into 0 ~ 3, 3 ~ 5, 5 ~ 15,> 15mm (this particle size range is adjustable). The granules after sieving are packed, shipped out and sold by the packaging machine.