Application of Large-inclination Belt Conveyor in Ceramsite
Date:2020-04-10 11:07:16
Author:admin
Views:
234
Traditional ceramsite rotary kiln often use ordinary belt conveyor to feed raw ceramsite materials after the granulation section into the kiln tail inlet. Because ordinary belt conveyors are limited by the inclination angle, the required length is generally longer, thereby increasing equipment footprint and construction cost.
The large-inclination belt conveyor is a device that can convey vertically at a large angle. The theoretical conveying angle can reach 90 °, and various bulk materials with a bulk density of 0.5-2.5t / m³ can be conveyed within the environment range of -25 ~ 40 ℃. It has large delivery volume, compact structure, small footprint, and is relatively simple to maintain. It is very suitable for the transportation of materials at the ceramsite kiln tail. At the same time, large-inclination belt conveyor has the features of low noise, more stable operation, better cleaning effect, and no pollution to the environment.
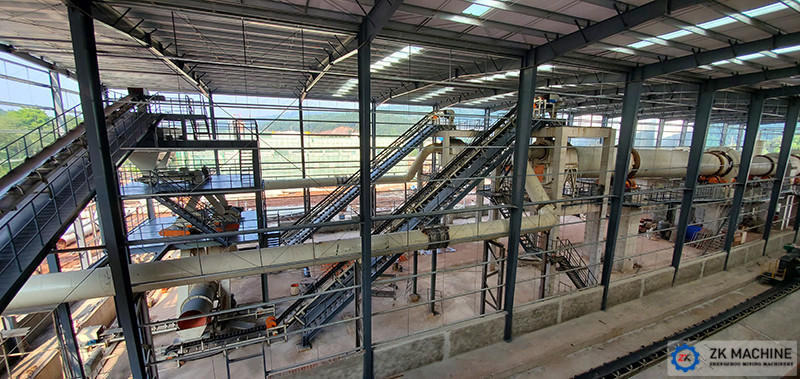
The large-inclination belt conveyor adopts a fully enclosed structure (including a hopper), and it will not affect the environment due to the material spilled during conveying. The entire fuselage is a sloping plate structure with integral bending of steel plates, and welding is instead of bolting connection. Frame wall panels (including lower horizontal section brackets, concave arc section brackets and upper horizontal section brackets) are all made of integrally bent steel plates to ensure the overall rigidity of the conveyor, and do not require a hoist frame and auxiliary support frame. As a part of the enclosed structure, the appearance is simple and beautiful; the mounting holes on the left and right wall plates are matched and combined drilling processes to ensure the installation accuracy.
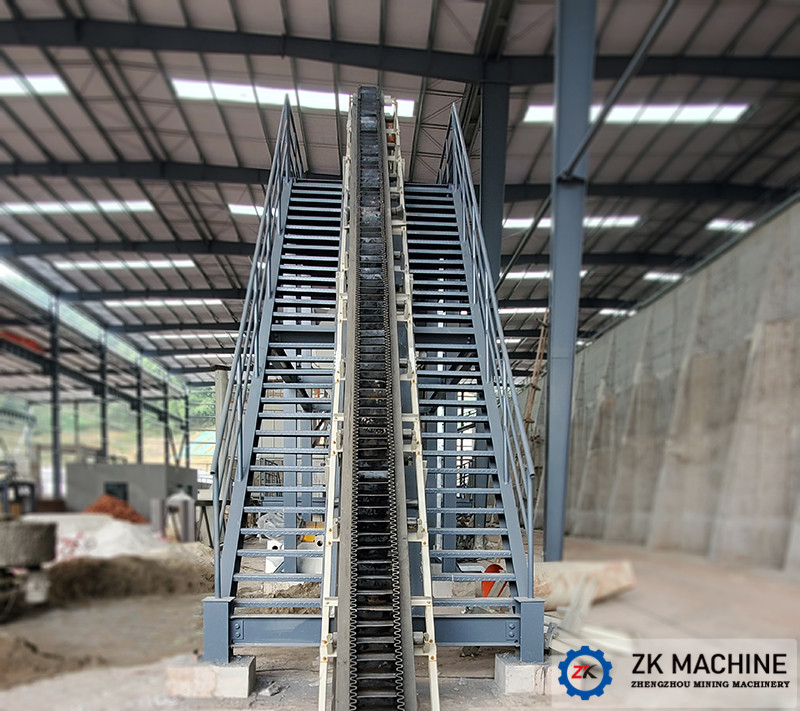
After welding, the large-inclination belt conveyor is then milled and combined drilling to eliminate welding deformation, ensure installation accuracy, and achieve optimal parallelism between the idlers, which ensures that the belt does not run off and increase the working life of the belt. The racks are connected by bolts through the connecting plate, which not only avoids welding deformation, but also installs quickly on site, which does not have high technical requirements for the installation workers. In addition, since the rack wall panel is a bent piece of steel plate, it is easy to add a dust-proof bottom plate and a dust-proof cover plate to form a fully enclosed structure for environmentally friendly production.