Process and Calcination Method for Zinc Oxide Rotary Kiln
Date:2019-09-15 17:14:30
Author:admin
Views:
156
Zinc oxide is a commonly chemical additive widely used in the production of plastics, silicate products, synthetic rubber, lubricating oils, paints, ointments, adhesives, foods, batteries, flame retardants and other products. Especially after the processing of zinc oxide through the rotary kiln, the application range is more extensive, because the processing methods of the equipment are various, which can fully satisfy the properties of zinc oxide and the needs of users. So, how does a rotary kiln process zinc oxide?
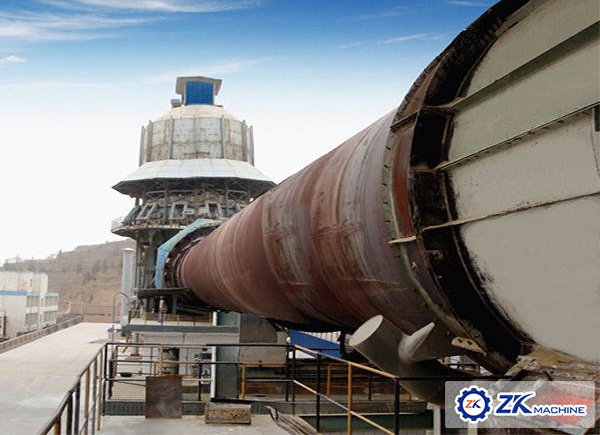
First, crush the zinc material and coke into less than 40 mesh pellets, uniformly mix them at a ratio of 1:0.30 to 0.35 to obtain a mixture, and then make into pellets having an effective diameter of 8-15 mm. Finally, put the pellets into rotary kiln for smelting. When smelting zinc ore containing zinc oxide in an amount of 15% to 25% or smelting zinc-containing industrial slag to produce zinc oxide, it has the characteristics of greatly saving coke or coal, smelting and obtaining good quality products, and improving productivity and small amount of nodulation.
Calcination methods of zinc oxide rotary kiln:
1. Direct reduction method
The direct reduction method is to pretreat the zinc oxide to be processed, and then perform a series of operations such as grinding, mixing, and pelletizing, and then enter the zinc oxide rotary kiln for oxide reduction and metal aggregation, and the clinker thus produced is selected gravity and sieved to obtain zinc minerals. At the same time, it can also be used in the zinc oxide rotary kiln ore furnace technology, which needs to be first dried, heated, calcined by the kiln, and then refined by the ore furnace to finally reduce the zinc material.
2. Blast furnace calcination method
After dehydration, calcination and agglomeration, the zinc oxide-containing ore is combined with coke and solvent to enter the blast furnace to obtain crude zinc, and the zinc material can be obtained after refining; In this step, it can also be operated by electric furnace. After dehydration and agglomeration, the zinc oxide ore is sent to an electric furnace to complete smelting with a certain amount of coke and solvent, and the obtained crude zinc oxide is re-refined to obtain zinc ore. In this process, the electric furnace operates to complete the smelting with carbon as a reducing agent.
The above is the calcination methods commonly used in zinc oxide rotary kiln. No matter which kind of calcination method, the temperature can be adjusted according to the amount of zinc oxide material, and finally achieve the user's desired goal. Moreover, the two calcination techniques have been proved by practice that the energy consumption is low, the product is dehydrated, decarburized and whitened, and the stability is good.